Typically, once a fan system is designed and installed, the fan operates at a constant speed. There may be occasions when a speed change is desirable, i.e., when adding a new run of duct that requires an increase in air flow (volume) through the fan. There are also instances when the fan is oversized and flow reductions are required.
Various ways to achieve change in flow are: pulley change, damper control, inlet guide vane control, variable speed drive and series and parallel operation of fans.
Pulley Change
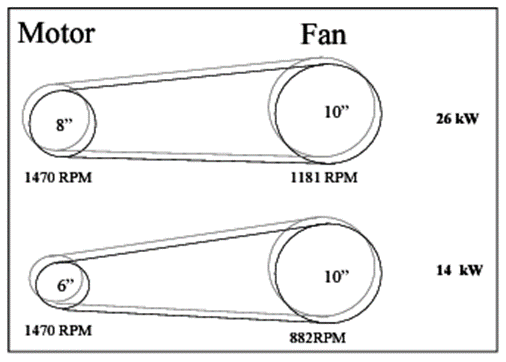
When a fan volume change is required on a permanent basis, and the existing fan can handle the change in capacity, the volume change can be achieved with a speed change. The simplest way to change the speed is with a pulley change. For this, the fan must be driven by a motor through a v-belt system. The fan speed can be increased or decreased with a change in the drive pulley or the driven pulley or in some cases, both pulleys. As shown in the Figure 1.1, a higher sized fan operating with damper control was downsized by reducing the motor (drive) pulley size from 8” to 6”. The power reduction was 12kW.
Damper Controls

Some fans are designed with damper controls (see Figure 1.2). Dampers can be located at inlet or outlet. Dampers provide a means of changing air volume by adding or removing system resistance. This resistance forces the fan to move up or down along its characteristic curve, generating more or less air without changing fan speed. However, dampers provide a limited amount of adjustment, and they are not particularly fan energy efficient.
Inlet Guide Vanes

Inlet guide vanes are another mechanism that can be used to meet variable air demand (see Figure 1.3). Guide vanes are curved sections that lay against the inlet of the fan when they are open. When they are closed, they extend out into the air stream. As they are closed, guide vanes pre-swirl the air entering the fan housing. This changes the angle at which the air is presented to the fan blades, which, in turn, changes the characteristics of the fan curve. Guide vanes are energy efficient for modest flow reductions – from 100 percent flow to about 80 percent. Below 80 percent flow, energy efficiency drops sharply.
Axial-flow fans can be equipped with variable pitch blades, which can be hydraulically or pneumatically controlled to change blade pitch, while the fan is at stationary. Variable-pitch blades modify the fan characteristics substantially and thereby provide dramatically higher energy efficiency than the other options discussed thus far.
Variable Speed Drives
Although, variable speed drives are expensive, they provide almost infinite variability in speed control. Variable speed operation involves reducing the speed of the fan to meet reduced flow requirements. Fan performance can be predicted at different speeds using the fan laws. Since power input to the fan changes as the cube of the flow, this will usually be the most efficient form of capacity control.However, variable speed control may not be economical for systems, which have infrequent flow variations. When considering variable speed drive, the efficiency of the control system (fluid coupling, eddy-current, VFD, etc.) should be accounted for, in the analysis of power consumption.
Series and Parallel Operation
Parallel operation of fans is another useful form of capacity control. Centrifugal fans in parallel can be additionally equipped with dampers, variable inlet vanes, variable-pitch blades, or speed controls to provide a high degree of flexibility and reliability. Combining fans in series or parallel can achieve the desired airflow without greatly increasing the system package size or fan diameter. Parallel operation is defined as having two or more fans blowing together side by side.

The performance of two fans in parallel will result in doubling the volume flow, but only at free delivery. As Figure 1.3 shows, when a system curve is overlaid on the parallel performance curves, the higher the system resistance, the less increase in flow results with parallel fan operation. Thus, this type of application should only be used when the fans can operate in a low resistance almost in a free delivery condition.
Series operation can be defined as using multiple fans in a push-pull arrangement. By staging two fans in series, the static pressure capability at a given airflow can be increased, but again, not to double at every flow point, as the above Figure displays. In series operation, the best results are achieved in systems with high resistances.
In both series and parallel operation, particularly with multiple fans certain areas of the combined performance curve will be unstable and should be avoided. This instability is unpredictable and is a function of the fan and motor construction and the operating point.
Factors to be considered in the selection of flow control methods
Comparison on of various volume control methods with respect to power consumption (%) required power is shown in Figure 1.4.
All methods of capacity control mentioned above have turn-down ratios (ratio of maximum–to–minimum flow rate) determined by the amount of leakage (slip) through the control elements.For example, even with dampers fully closed, the flow may not be zero due to leakage through the damper. In the case of variable-speed drives the turndown ratio is limited by the control system. In many cases, the minimum possible flow will be determined by the characteristics of the fan itself.Stable operation of a fan requires that it operate in a region where the system curve has a positive slope and the fan curve has a negative slope.
The range of operation and the time duration at each operating point also serves as a guide to selection of the most suitable capacity control system. Outlet damper control due to its simplicity, ease of operation, and low investment cost, is the most prevalent form of capacity control. However, it is the most inefficient of all methods and is best suited for situations where only small, infrequent changes are required (for example, minor process variations due to seasonal changes. The economic advantage of one method over the other is determined by the time duration over which the fan operates at different operating points. The frequency of flow change is another important determinant. For systems requiring frequent flow control, damper adjustment may not be convenient. Indeed, in many plants, dampers are not easily accessible and are left at some intermediate position to avoid frequent control.
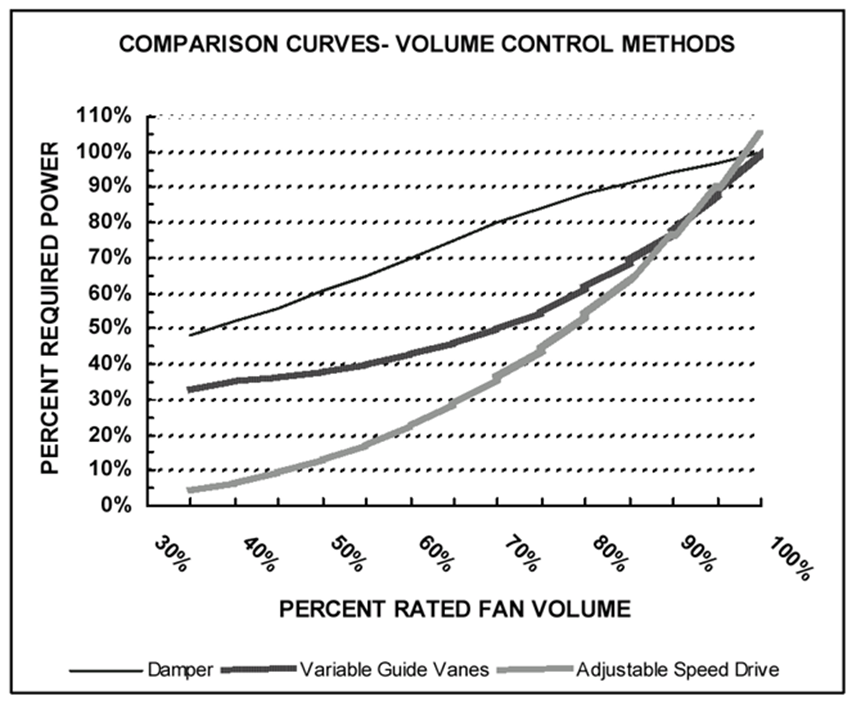
Related Posts:
Most fans are sized to handle the largest expected peak design condition. Because normal operating conditions are often well below these design conditions, air-moving equipment is often oversized, operating below its most…
Another component of the prime mover is the motor controller. The controller is the switch mechanism that receives a signal from a low power circuit, such as an on/off switch, and energizes or de-energizes the motor by…