Blower is power consuming machine, where large volumes of gas or air at low pressure are required. According to the “Compressed Air Institute”, it is a machine to compress air or gas by centrifugal force to a final pressure not exceeding 2.4 bar. It is not water cooled, as the added expense of the cooling system is not justified in view of the relatively slight gain at this pressure. Centrifugal blowers are generally used for large air supply systems for reduced noise and maintenance. Here are few applications of blowers enumerated as High pressure air blower, Sewage aeration blower, Scavenging two cycle diesels blower, Cupola blowers, Blast furnace gas blowers, Water gas blowers, Municipal gas plant blowers, Cock plant exhausters and blowers, Airplane superchargers and Circulators.
IMPELLER
According to rotating blade type the impeller are classified as radial, forward and backward type. The blade exit angle decides the type of impeller. The pressure rise and flow rate in blower depends on the peripheral speed of the impeller and blade angle.
In backward impeller the exit blade angle is less than 900 . The channel of blade is gradually expanding, so that the relative airflow will decelerate gradually, while passing through the channel of blade.
Compared to other two types of impeller the backward curved impeller has maximum efficiency at design condition and at the design point the energy coefficient which is the measure of pressure rise in the blower is less in case of the impeller compared to other two.
In radial impeller the exit blade angle is equal to 900 . At the maximum efficiency condition the flow coefficient is higher for this type of impeller.
In forward impeller the blade tips incline towards the direction of rotation and exit angle is greater than 900 , which is a very large blade angle. For the same size & speed these types of impellers have higher flow rate compared to others. As tangential velocity is very large at the exit, this gives higher stage pressure rise compared to other two and it has maximum energy coefficient. As the selection of the impeller is preliminary factor for Blower system.
OUTLET SYSTEM
Fluids leaves the impeller at an higher absolute velocity as compare to that in the discharge pipe, therefore this fluid is collected by outlet system without affecting it’s performance. Outlet system reduces the flow velocity, by improving the outlet pressure. These outlet systems have an annular space outside the impeller before the volute or diffuser ring. This annular vaneless space decreases the non-uniformities and turbulence of flow entering the volute as well as the noise level. There are three types of outlet system 1) Vaneless Diffuser 2) Vaned Diffuser 3) Volute or Spiral Casing.
VANELESS DIFFUSER
In this fluid is diffused in the vaneless space around the impeller before it leaves the stage through a volute. Diffusion occurs from smaller diameter to larger diameter and gain in static pressure occurs. As diffusion is directly proportional to diameter ratio it gives relatively large 5 size diffuser, which is the limitation of this outlet system. Besides this it has a lower efficiency. This type of application generally used for large size compressor, as it does not suffer from blade stalling and shockwaves.
VANED DIFFUSER
The fluid from the impeller is discharged through a vane diffuser for 1200W variable speed industrial air blowers. In this diffusion achieved by means of diffuser vanes, which results smaller size diffuser. Also the vanes provide greater guidance to the flow in the diffusing passages. The provision of diffuser in a blower can give a slightly higher efficiency (4-5%) than a blower with only a volute casing. Every diffuser blade ring is designed for given flow condition at the entry where optimum performance is obtained. Therefore at off- design condition the diffuser will give poor performance on account of mismatching the flow.
VOLUTE CASING
The purpose of the blower casing is to guide the fluid from the impeller or diffuser and convert into pressure, the flow with high kinetic energy is discharge from impeller and leads gas or air away. The Volute surrounds the impeller and whose cross-sectional area increases from a minimum at the tongue or cutwater to the throat. The tongue represents the nearest part of the casing to the impeller and is aligned into the general direction of the flow leaving the impeller as shown in figure: 1.1. The casing plays an important part in locating best efficiency point by virtue of its hydraulic loses and its ability to restrict the flow against given head without incurring any additional losses. Flow leaving out of the casing can tangential or radial as shown in figure: 1.1a. Finally flow leaving out of the casing is through the volute throat as shown in figure: 1.1b. Tongue and throat position is very important in the design of volute casing. Velocity components in the volute is shown in 1.1c and change in cross-section area of volute at different radius. As cross-section area of volute casing goes on increasing from tongue region to throat.
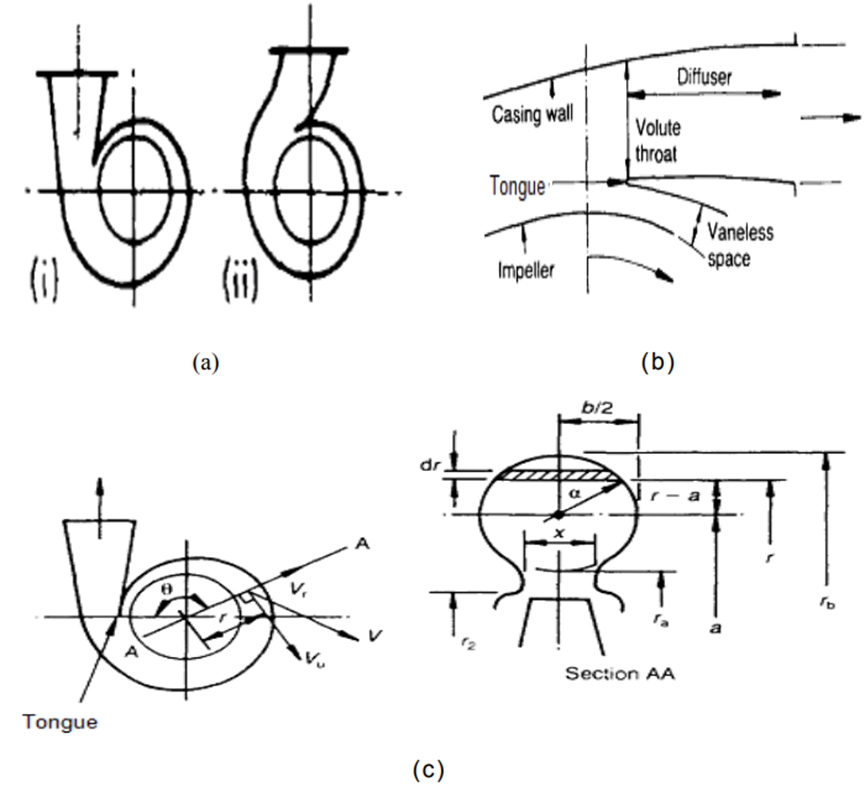
Related Posts:
A centrifugal blower impeller have backward swept blades, radial tipped blades or forward swept blades as shown in figure: 1.1 below. The inlet and outlet velocity triangles are also shown accordingly in the figure. Under ideal conditions, the…
Fans are constructed from many different materials, and like everything else, there are pros and cons to any option. 1) Heavy solid-blade fans may experience extended starting times due to the high inertia load that the…